ちょっと昔のパンチプレス事情
当たり前に使われているタレットパンチプレスですが
ネット環境のおかげで加工データが簡単にパソコンから機械へ転送できたり
加工データを元にタレパンのタレットがクルクル回って金型で打ち抜き加工をしたり
座標に向かって自由自在に動いているのを眺めていると、ふと
「昔のタレパンって、加工どうしてたんやろ…データは?手打ち?」
と疑問が湧き出てきたのでいろいろと上司に質問してみました!
【位置決めの治具】
位置決めの治具を制作、プレス機にパンチセット金型をセットして打ち抜き加工。
毎回プレスをする個所の位置決めのためだけに治具を制作しないといけなかったらしく
プレス個所が多いと一つの製品に対して治具が複数必要だったり…今は加工データを呼び出して
スタートボタンを押せば勝手に加工されて勝手に原点に帰ってきますからね!
またタップ加工もタップ専用の機械があり、最初にマニュアル操作でタップ位置の座標を機械に記憶させ
そこから記憶させた座標に向かってオートメーションで加工していたそうです。
大ロットだった場合ボール盤で一つひとつタップ加工…より、はるかに効率的かと思いますが
今の機械を知っていると、やはり加工にかかる時間と工程数の多さにビックリします。

↑タップ加工の機械↑
【加工データが紙テープ】
パンチプレスの自動化が進んでも今のようなネット環境ではなく
弊社ではCADCAMで作ったデータを紙テープパンチャーで紙テープに
加工データとして落とし込み、その紙テープを機械に読み込ませて加工していたそうです。
懐かしく感じる人もいるのではないでしょうか?私は全然知らない代物でした。
ここからフロッピーに変わり、今のネット環境へと変化していったということに文明を感じます。
一巻きの未使用紙テープが約270メートル、記録できるデータ容量が67キロバイト程しかなく
加工工程数が多いと、紙テープがとんでもない長さになったとか((+_+))
紙テープにしろフロッピーにしろ、何がどのデータなのか管理が大変だったこともうかがえます。
↓紙テープパンチャー↓
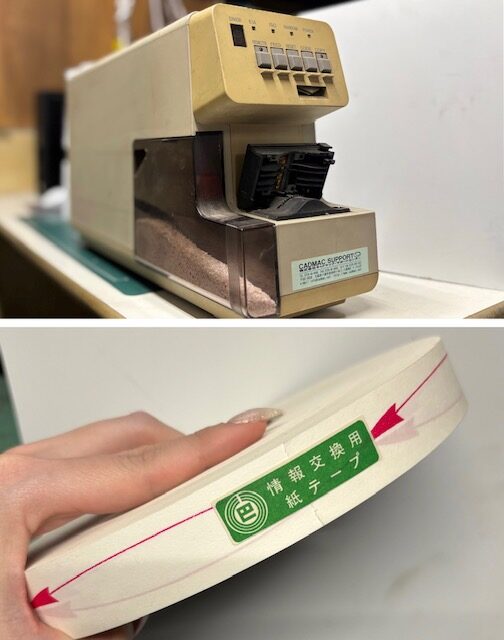
パソコンへ繋ぐ線がないため使用できないのですが、社内で大切に保管されていました。
製造業界の最新知識を知るのも楽しいですが、昔のことを知るのもなかなか新鮮ですね(`・ω・´)